預(yù)制疊合板構(gòu)件是裝配式建筑的重要組成部分,在工序中造成的疊合板裂縫的問題不容忽視;诠こ虘(yīng)用和結(jié)合構(gòu)件生產(chǎn)過程,對(duì)疊合板裂縫產(chǎn)生原因進(jìn)行分析并提出相應(yīng)控制措施。
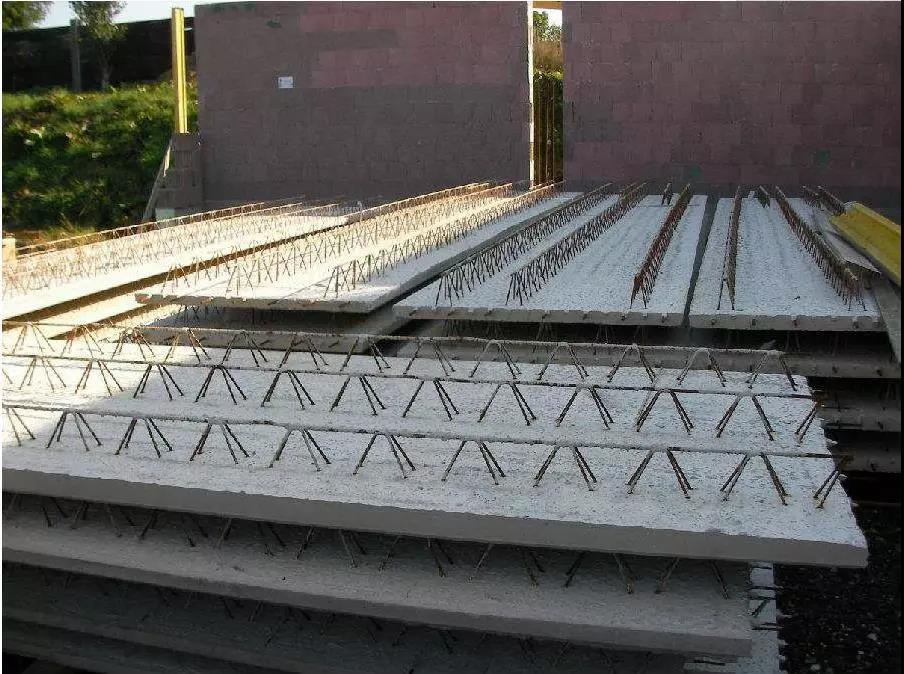
1.什么是疊合板?
疊合板是疊合構(gòu)件的一種,是由預(yù)制混凝土構(gòu)件(或既有混凝土結(jié)構(gòu)構(gòu)件)和后澆混凝土組成,以兩階段成型的整體受力結(jié)構(gòu)構(gòu)件。
施工時(shí),現(xiàn)場先安裝預(yù)制混凝土底板,以其為模板,輔以配套支撐,再澆筑混凝土疊合層(即上部現(xiàn)澆混凝土部分),當(dāng)上層混凝土與預(yù)制板形成統(tǒng)一整體后,共同承擔(dān)上部的荷載。這種結(jié)構(gòu)優(yōu)勢明顯,結(jié)合了現(xiàn)澆結(jié)構(gòu)和預(yù)制結(jié)構(gòu)的優(yōu)點(diǎn),在保證結(jié)構(gòu)整體性的同時(shí),又能滿足構(gòu)件工業(yè)化進(jìn)度的要求,而且節(jié)約了大量的模板支拆,降低了施工成本,是非常具有拓展?jié)摿Φ臉前逍问健?/p>
2.產(chǎn)生裂縫的工序
疊合板預(yù)制層的工藝流程如下:模臺(tái)清理→組模→涂刷緩凝劑、脫模劑→鋼筋綁扎→水電預(yù)埋→混凝土澆筑→振搗→預(yù)養(yǎng)→拉毛→養(yǎng)護(hù)→脫模起吊→運(yùn)輸?shù)匠善范逊艆^(qū)(根據(jù)設(shè)計(jì)要求增設(shè)水洗)。
根據(jù)經(jīng)驗(yàn),可能產(chǎn)生裂縫的主要工序有振搗、拉毛、養(yǎng)護(hù)、拆模、吊運(yùn)、堆放等。
3.疊合板澆筑、振搗、拉毛
成因分析:
1.混凝土澆筑后,目前在PC自動(dòng)流水線上,預(yù)制構(gòu)件主要采用振動(dòng)臺(tái)進(jìn)行振搗。采用振動(dòng)臺(tái)振搗,震動(dòng)頻率快、效率高,僅需15-30S便振搗完成。由于設(shè)備操作人員的經(jīng)驗(yàn)不足,往往出現(xiàn)過震,產(chǎn)生離析現(xiàn)象,造成裂縫的產(chǎn)生。
2.預(yù)制構(gòu)件使用的混凝土坍落度較小、黏度較大,采用固定模臺(tái)生產(chǎn)時(shí),用振搗棒振搗,容易過度振搗桁架,且因振搗點(diǎn)位少,很容易導(dǎo)致桁架外露筋處混凝土嚴(yán)重泌漿甚至局部離析,造成沿著桁架筋方向的裂縫。
控制措施:
采用振動(dòng)臺(tái)振搗混凝土,對(duì)設(shè)備操作人員進(jìn)行交底,明確操作要求。采用人工振搗時(shí),振搗棒應(yīng)橫放振搗,同時(shí)注意振搗時(shí)間,避免局部過振和振搗桁架。在施工作業(yè)過程中,混凝土未達(dá)到起吊強(qiáng)度前,嚴(yán)禁踩踏桁架筋。
4.疊合板養(yǎng)護(hù)
成因分析:
目前裝配式建筑的構(gòu)件在工廠中的養(yǎng)護(hù)主要采用蒸汽養(yǎng)護(hù)的方式,蒸汽養(yǎng)護(hù)分為靜停、升溫、恒溫、降溫四個(gè)階段,混凝土逐漸硬化和增長強(qiáng)度其實(shí)是水化反應(yīng)的過程,而水化反應(yīng)對(duì)溫度、濕度有著較高的要求。因此,當(dāng)溫度、濕度達(dá)不到要求時(shí),因混凝土收縮很容易使構(gòu)件產(chǎn)生裂縫。
控制措施:
在預(yù)養(yǎng)護(hù)時(shí)期,控制預(yù)養(yǎng)溫度不低于10℃,混凝土終凝且在灌筑結(jié)束4~6h后才可升溫;升溫時(shí)控制升溫速度,不宜大于10℃/h;恒溫期間混凝土內(nèi)部溫度不宜超過60℃,最大不得超過65℃,恒溫養(yǎng)護(hù)時(shí)間應(yīng)根據(jù)構(gòu)件脫模強(qiáng)度要求、混凝土配合比情況以及環(huán)境條件等通過試驗(yàn)確定;降溫期,保證降溫速度不大于10℃/h;還應(yīng)盡量保證各部位溫度一致,溫差不宜大于15℃。
5.疊合板拆模
成因分析:
構(gòu)件養(yǎng)護(hù)結(jié)束后,裝配式建筑的構(gòu)件強(qiáng)度如未達(dá)到拆模的強(qiáng)度要求而強(qiáng)制拆模,可能會(huì)因?yàn)閺?qiáng)度原因,使構(gòu)件側(cè)面產(chǎn)生裂縫,后期存放、成品保護(hù)不到位,這些裂縫會(huì)繼續(xù)延展,最終在板面上形成不同方向的裂縫。
控制措施:
拆模前應(yīng)采用回彈儀監(jiān)測疊合板強(qiáng)度,待疊合板達(dá)到設(shè)計(jì)強(qiáng)度要求的75%或者設(shè)計(jì)圖紙要求的強(qiáng)度后,方可拆模。拆模應(yīng)按要求模具的組裝工藝以及拆模要求進(jìn)行,嚴(yán)禁暴力拆模。
6.疊合板起吊、轉(zhuǎn)運(yùn)
成因分析:
疊合板吊點(diǎn)位置是根據(jù)疊合板的形狀、大小,通過受力分析、彎矩計(jì)算并參考國家規(guī)范、圖集最終確定的,因此較大的疊合板往往有六點(diǎn)、八點(diǎn)起吊不等。由于疊合板是平起,且厚度僅60mm,為防止疊合板起吊轉(zhuǎn)運(yùn)過程受力不均勻,有專用的平衡架輔助起吊。
但在實(shí)際操作過程中,往往出現(xiàn)構(gòu)件直接起吊不采用平衡架;設(shè)計(jì)要求六點(diǎn)、八點(diǎn)起吊但生產(chǎn)時(shí)依舊四點(diǎn)起吊;不按照圖紙規(guī)定的吊點(diǎn)位置起吊等不規(guī)范行為。這些不規(guī)范操作會(huì)造成構(gòu)件在吊運(yùn)途中因撓度過大而產(chǎn)生裂縫。構(gòu)件從工廠到堆場再到現(xiàn)場存在多次轉(zhuǎn)運(yùn),這種不規(guī)范操作會(huì)加深疊合板裂縫,最終裂縫將延伸至整塊板,更嚴(yán)重的會(huì)形成貫穿裂縫,致使整塊板報(bào)廢。
控制措施:
加強(qiáng)對(duì)工廠的管理,規(guī)范吊裝、轉(zhuǎn)運(yùn)操作流程,嚴(yán)格要求工人按照設(shè)計(jì)圖紙規(guī)定的吊點(diǎn)數(shù)量與位置,使用專業(yè)吊具進(jìn)行吊運(yùn),要慢起慢落,避免與其他物體相撞,并要確保起重設(shè)備的吊鉤位置、吊具及構(gòu)件重心在垂直方向上重合,吊索與構(gòu)件的水平夾角不應(yīng)小于45度,不宜小于60度;減少不必要的吊運(yùn)次數(shù);保證構(gòu)件達(dá)到設(shè)計(jì)強(qiáng)度的75%或設(shè)計(jì)圖紙要求強(qiáng)度后,再吊運(yùn)構(gòu)件。
7.疊合板堆放、運(yùn)輸
成因分析:
1.在實(shí)際碼存放過程中往往出現(xiàn)很多不規(guī)范的堆放方式,如:疊合板堆放過高,某些工廠為了節(jié)約場地,疊合板碼放高達(dá)8-10層;疊合板碼放不規(guī)整,大板壓小板;墊木擺放隨意、不規(guī)范,上下層墊木不在同一垂直線上,而且沒有按照要求擺放,超長超寬的疊合板依舊只放四塊墊木。這些行為造成疊合板支撐受力不均勻,進(jìn)而導(dǎo)致裂縫產(chǎn)生。
2.疊合板因運(yùn)輸原因產(chǎn)生裂縫的情況,與堆放時(shí)產(chǎn)生裂縫的原因基本一致,但在運(yùn)輸中難免會(huì)有道路不平而引起汽車顛簸,這樣會(huì)產(chǎn)生動(dòng)荷載,若固定疊合板的方式不牢固,則很難約束疊合板,疊合板之間發(fā)生相對(duì)位移,最終導(dǎo)致疊合板產(chǎn)生裂縫。
控制措施:
1.每垛疊合板尺寸規(guī)格應(yīng)盡量統(tǒng)一,嚴(yán)禁大板壓小板;保證每層支點(diǎn)在同一垂直線上,避免因支點(diǎn)上下不一而產(chǎn)生剪切裂縫;支點(diǎn)應(yīng)放置在桁架筋側(cè)邊,板兩端(至板端200mm)及跨中位置均應(yīng)設(shè)置支點(diǎn)且間距不大于1.6m;堆放層數(shù)不宜超過6層;構(gòu)件生產(chǎn)完成后,應(yīng)盡早運(yùn)至現(xiàn)場安裝,在堆場堆放時(shí)間不宜超過2個(gè)月。
2.應(yīng)在支點(diǎn)處綁扎牢固,防止裝配式建筑的構(gòu)件在運(yùn)輸途中移動(dòng)或跳動(dòng)。同時(shí),在底板的邊部或與繩索接觸的混凝土,應(yīng)用襯墊加以保護(hù)。
結(jié)語 :
隨著我國裝配式建筑的不斷發(fā)展,裝配式疊合板的質(zhì)量問題已經(jīng)成為人們關(guān)注的焦點(diǎn),相信只有從疊合板生產(chǎn)工序的各個(gè)環(huán)節(jié)進(jìn)行把控,同時(shí)加強(qiáng)對(duì)工人的專業(yè)技能培訓(xùn),才能有效預(yù)防疊合板開裂現(xiàn)象的發(fā)生。